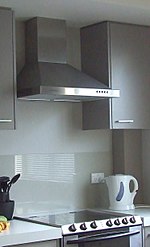
An extractor hood (U.K.) or range hood (U.S.), also known as a kitchen hood, stove hood, exhaust hood, cooker hood, extraction hood, cooking canopy, ventilation hood, extractor fan or electric chimney, is a device containing a fan that hangs above the stove or cooktop in the kitchen. It is used to remove airborne grease, combustion products, smoke, odors, heat, and steam from the air by a combination of filtration and evacuation of the air.
An extractor hood consists of three main components: a skirt or capture panel to contain the rising gases (also known as the "effluent plume"), one or more grease filters, and a fan for forced ventilation.
Grease removal from the extracted air stream is facilitated by filters mounted in the extractor hood. Many different types of filters are commercially available but most use the same mechanical action to capture the airborne grease and other pollutants. The ultimate goal of the filter is to cause the grease particles to combine together to form larger particles and to come into contact with the surfaces of the filter and stick to them. The mechanics employed by the filter to cause this to happen are a combination of causing the air to change direction, causing the air to change velocity and causing the air to rotate or vortex rapidly, the resultant centrifugal and centripetal forces cause the grease particles to collide, combine and adhere to the baffles or course filter medium contained within the filter frame. As the grease builds up, it runs down the filter by gravity and usually into the extractor hood frame that the filters are mounted in. This acts as a trough which holds the grease, or, depending on the hood design, diverts it into a collection tray.
Mechanical baffle type filters vary greatly in their efficiency at grease capture and removal. All mechanical filters are more efficient at removing larger grease particles (larger than 10 micron). With smaller particulates they are increasingly ineffective. The grease that escapes through the filters is prone to collecting in the ducting and the fan unit where it is a fire hazard and can also cause mechanical failure.
Filters should also provide a measure of flame retardation to prevent a fire under the hood spreading into the plenum area of the hood and onward into the ducting and fan. The most common material for filter construction is stainless steel which is resilient to high temperatures, chemical action and is hygenic and easy to clean.
Filter efficiency is usually a trade off against system static pressure. The finer the filter medium, the more resistance it presents to the air flowing through it. This then means larger and more powerful fans must be used to maintain sufficient air extraction volume. Some extractor systems use two or three stages of filters to improve grease removal efficiency.
Activated carbon filters are sometimes used as the final filter stage. All the grease particulates must be removed from the extracted plume before this stage. Carbon filters are used to remove odors, not grease. The activated carbon is rendered useless if it becomes coated in grease deposits. Once impregnated it cannot be effectively cleaned and replacements are expensive. For these reasons, carbon filters are best avoided in grease applications if possible.
Other methods of grease removal found in extractor hoods are water wash systems. These hoods use a fine cold water mist to cool the airflow for the full duration of the extraction operation time. This cooling causes the grease particles to stick together more readily and form larger particles. By a system of internal baffles, these larger particles then adhere to the internal surfaces of the hood. The water spray collects in a trough at the lowest point in the hood where it then runs away to drain. Some water wash hoods have an automated hot water and detergent wash cycle to remove the accumulated grease at the close of every day. The water consumption of these hoods is around 0.66 liters per minute per running meter of hood, according to the manufacturers specifications. This figure can be considerably higher for older hoods with worn, damaged or missing water nozzles.
Water wash canopy hoods have been around since the 1970's when water consumption and regular introduction of industrial strength surfactants into the city drainage system was not a burning issue. They are still manufactured today, but in a modern climate of ecological awareness this method of operation is not always considered acceptable. There are retrofit devices available for these canopy hoods to decrease their water consumption to a more acceptable level. The strength of the water wash hood system is its inherent fire resilience and its automatic cleaning ability. They are up to 90% efficient at grease removal which is higher efficiency than most filter hoods. The disadvantages are that a relative complex control system is required for the water systems. The hot water wash uses a large amount of water in a very short time and consequently requires a dedicated water heater cylinder. Complex plumbing and large diameter copper water drains for the hood add considerably to the installation costs and the waterproof hood is expensive to manufacture. The hot wash system consumes around half a liter of detergent per day, depending on the length of the hood.
There are variations on the water wash hood theme that recycle the water around a pipe circuit by means of a pump. These consume far less water and retain all the benefits of the water wash system. They do however still consume detergent and are very prone to pump failure caused by grease build-up should the detergent ever run dry. They also trade off the reduction in water consumption with the power consumption of the pump which is considerable at 1-1.5 Kilowatts at a poor power factor.
Hoods employing more than one of the filtration methods are not uncommon in commercial applications.
Extractor hood systems accumulate grease on the internals of the hood, ducting and fan. There is a large volume of air flowing through the system during its operation. An ignition source is all that is needed to complete the recipe for a roaring fire. The ignition source can easily com from general cooking practices or a kitchen equipment fault resulting in an oil fire under the hood. As a method of fire prevention in addition to the filters, extractor hoods should also have an automatic fire damper before the duct work connection or spigots. This fire damper is usually held open by a heat sensitive link against a spring tension. When the temperature rises to a dangerous level (above 120 degrees Celsius)the link separates and the damper snaps closed to prevent the spread of flame. Some extract hood ducting systems also have a water sprinkler system internally installed as a further fire resistance measure. Additionally fire suppression systems are often installed in the extractor hood below the filters to extinguish kitchen equipment fires below it.
Many types of air movement fans can be used on extraction hood systems. Different types of fans are used for different applications; Tangential (Forward Curved Centrifugal) Fans
Tangential blower fans are essentially a forward curved centrifugal blade and are suitable for air systems requiring high volumes at very low system static pressures. They are quiet in operation which usually means extra sound attenuators will not be necessary. They have a long, wheel shaped impeller with many forward curved blades which looks a little like an elongated hamster wheel. The forward curve of the blades tends to promote grease build-up on the leading face of the blades when they are used on Kitchen canopy extract systems, this can cause imbalance of the blade set, eventually resulting in vibration and premature mechanical failure. The construction of this type of fan blade makes it very difficult to keep clean in a greasy environment. The static pressure across the filter in the canopy hood is usually too high for a tangential blade to be effective in this application. The filter static pressure also increases as it becomes impregnated and saturated in grease from the cooking processes under the hood which further resists the air flow and compounds the inefficiency of this type of fan blade. Tangential blower fans are occasionally found in domestic extraction hoods but are more commonly used in mid-wall air conditioners.
Forward curved fans are sometimes used an integral part of an ecology filtration unit. The theory is that the various stages of filters prevent the fan blades ever coming into contact with the airborne grease but in practice this is not always the case.
Forward curved fan blades can be built to operate under higher static pressures (up to around 1000 Pascal’s) but their air delivery volume is generally lower. They come in single and double inlet configurations. The drive motor can be direct drive configured or mounted external to the fan housing with pulley wheels and drive belts connecting the main fan drive shaft.
The rotating blade causes air to be centrifugally thrown into the scroll or snail shaped fan housing. Whilst the blades discharge evenly all around in a radial fashion, the shape of the housing helps to facilitate discharge in one direction. Suction side air is drawn horizontally into the center of the blade set which means a centrifugal fan will always change the direction of the airflow by 90 degrees. This means they are difficult to configure as an in-line fan inside the ceiling space. The direction and height change between suction and discharge ducting makes them more suited to rooftop installation.
Unlike an axial fan, the dynamics of a centrifugal fan render it completely ineffective when it runs in reverse rotation.
Although they are not well suited to extraction applications, forward curved fans are very useful as make-up air or supply air fans where long ducting runs are necessary and filtration units are incorporated to purify the air causing higher static pressure which can rule out the use of an axial fan.
Axial
An axial fan has a blade set that looks similar to an aircraft propeller. Between three and sixteen blades are attached to a center hub which mounts on a drive shaft. The more blades on the hub, the higher the pressure the fan can handle. The cross sectional profile of the blade is slightly curved with a thicker and more rounded leading edge. This gives it aerodynamic properties similar to an aircraft wing. An axial blade set will move air in either direction depending on which way it is rotated but, due to the blade profile, it will be more efficient and less noisy in the correct direction. Reverse rotation can cause motor overload damage. The blade set can be fitted directly onto the motor shaft and the motor would be pad mounted inside the ducting. Alternatively the blade can be fitted to a shaft with a pulley wheel and drive belts connecting it to an externally mounted motor.
With axial fans, usually the blade angle is adjustable. Care must be taken when adjusting them however to ensure that the drive motor is not overloaded. Axial fans are robust, easy to source ‘off the shelf’ in all shapes and sizes, mechanically simple and therefore reliable, compact in size and inexpensive to purchase. They come in long tube, short tube and plate configurations.
Axial fans move large volumes of air but have limitations when it comes to high static pressures. A general purpose axial fan of 800mm diameter blade set with 14 blades rotating at 1440 RPM will operate up to 450-550 KPa static pressure at the high end of its operating curve. They also generate high noise levels and usually the higher the static pressure, the higher the noise. Although axial fans are relatively cheap, when the cost of a suction and discharge side noise attenuators are factored in, they can work out more expensive than a different type of fan that is quieter in operation and doesn’t require additional attenuation. General purpose axial fans are available in rotation speeds between around 800 and 2500 RPM. Axial fans with a rotational speed of less than 600 RPM are only suitable for use in very low pressure applications or 'free air'.
When an axial fan operates under low pressure, the air flows at right angles into and out of the blade set. The path of the airflow, apart from some rotation, suffers minimal deviation which allows the fan to operate efficiently and fairly quietly. As the pressure across an axial blade set increases, more centrifugal action is suffered by the air which increases vortexing and causes more operating noise. This centrifugal action reduces the efficiency of the fan and the velocity of the air traveling through it. An axial blade of around 800mm diameter rotating at 1400 RPM can generally only be effective up to around 450 Pascal’s of system static pressure. To reduce the rotating of the air stream and the vortexing effect, some axial fans incorporate a set of guide vanes on the suction side. These fans are often referred to as vane axial fans. The addition of these vanes will slightly improve their efficiency and pressure handling ability.
When the pressure drop across an axial fan increases, so does the absorbed power and consequently the motor running current. This means the size of the motor cannot be too closely matched to the predicted blade power consumption when the fan is in ideal running conditions. Allowances must be made for the worst case power consumption when sizing the motor which can result in low power efficiency if the motor is running at less than 80% of is full load capability under normal operating conditions.
Axial fans in kitchen extraction systems nearly always have adjustable blades. By loosening the hub the blade angle can be altered to increase the extraction system performance. This offers a certain amount of flexibility; the angle can be reduced for better high pressure performance or increased for higher volumes with low pressure applications. The limitations of the drive motor must be taken into account before blade set adjustment and motor running current tests must always be performed afterwards. Increasing the blade angle will only produce increased airflow to the point where the static pressure in the extraction system becomes too high for the blades to handle. Further angle increments from this point on will then result in lower airflow as the efficiency plummets. The motor thermal overload protection should also be readjusted after blade angle alterations.
Axial blades have a far greater velocity at their outer tip. The velocity decreases toward the center of the blade set. This means that the majority of air flow takes place at the blade tips. Even though the solid center hub of the blade set and a large pad mounted drive motor presents what appears to be a considerable obstacle in the path of the airflow, very little air resistance is actually caused by these items and the pressure drop within the fan unit itself will be less than 50 Pascal’s.
The high speed rotation of the axial blade set causes grease that adheres to the blades to be centrifugally slung onto the fan housing where it collects. This build-up of grease will eventually interfere with the blade tips as they rotate. This can cause mechanical failure of the blade set, bearing failure due to high running temperatures or complete electrical failure of the motor. It is essential that the fan unit be periodically removed and cleaned.
Backward Curved Centrifugal Fans
This type of fan has a blade set similar to a forward curve centrifugal fan except the blades are inclined backward into the airflow. There are usually a lot less blades in a backward curve fan than in a forward curved unit but the snail shaped housing is still often utilized for single direction discharge.
Backward curved blades are very efficient, quiet and suited to higher pressure applications (1500 Pascal’s). They are less prone to grease build-up on the blade surfaces and considerably easier to clean in situ than a forward curved fan. The airflow changes direction by 90 degrees for the same reasons as a forward curved blade set but there are various ‘straight through’ configurations available in smaller sized fans.
Backward curved fans have an advantage over other types of fans in that the absorbed power of the blade set does not increase significantly even when it is run outside of its intended design limits. This means that no over sizing of the drive motor is necessary to allow for a worst case scenario such as fire dampers closing or doors sticking on the vertical discharge unit (VDU).
Mixed Flow Fans
Mixed flow fans are a happy medium between axial fans with their high flow volumes and centrifugal fans with their good pressure handling capabilities. They will provide good flow rates up to around 750 Pascal’s of system static pressure. They inherit the non-overloading characteristics of the backwards curved fans but cannot be used in reverse rotation. They also produce relatively little noise and can often be specified without additional sound attenuators. As with all fans the closer they are run to their ideal design static pressure, the less noise power they generate. Their cost is on a par with, or slightly higher than, other centrifugal fans but considerably more expensive than axial fans. There are medium and larger sized mixed flow fans that have adjustable blade sets to allow for some performance characteristic tuning similar to axial fans.
A mixed flow fan discharges diagonally from the blade set. This is to be expected from a fan which is part way in characteristics between an axial flow fan and a centrifugal fan with radial discharge. This makes them easily suited to a straight through type configuration and they are often encountered mounted in-line in a straight ducting run.
All blades will have a performance graph that is available from the blade manufacturer. This graph will indicate the blades performance under different static pressures, various blade angles and different rotational speeds where applicable. The ideal is to specify a fan blade that will be running somewhere around the middle of its performance curve with the predicted volumes required and static pressure of the system it will be installed in. A fan blade will give smooth and predictable behavior on the middle area of its operational curve. If the blade is running at the very top of its curve, small changes in static pressure will have large effects on the air volume being moved. This means that partly dirty filters could be the difference between satisfactory operation and a kitchen full of smoke.
The hub of the blade set has a hole for mounting it onto the drive shaft or motor shaft. There is usually a woodruff key arrangement, a locking nut or bolt and a washer to prevent movement between, or separation of, the blade and shaft during operation. The hub should be a good interference fit on to the shaft to prevent movement and vibration which would lead to heat generation, accelerated wear of the components and premature failure. Mechanical or hydraulic puller tools are often required to separate a blade from the shaft.
An inlet cone is an air guide designed to put the incoming air into the right area of the fan blades whilst reducing or preventing eddy currents and air rotation on the suction side of the fan. This will improve the overall efficiency of the fan unit and keep the noise power generated to a minimum. With a centrifugal fan the inlet cone should overlap the blade set internally and should be toleranced as close as reasonably possible keeping the gaps between the two to a minimum. It should however be noted that if contact friction develops between the stationary inlet cone and the rotating blade set, the resulting heat generated can cause a fire hazard and spontaneous combustion, especially with grease build-up in an extraction system that is due for cleaning. In the case of a tube type axial fan, no separate inlet cone is used. The tubular housing in this case performs some of the functions of an inlet cone. With a plate axial type fan the diaphragm plate is manufactured with a conical profile in the center to efficiently guide the air onto the blades.
All extraction systems should have a suction side blade guard on the fan to prevent foreign debris such as cleaning rags and hygiene hair nets going through the fan blades. The guards are usually a wire structure resembling a spider web, they do tend to collect grease which can cause high system static pressures when they get dirty so must be cleaned regularly. If the fan is near the discharge point of the extraction system and physically accessible through the vertical discharge unit (VDU), a discharge side guard should also be installed for safety, effectively enclosing the blade set entirely. Where possible, guards should be removable with the fan blades still in situ to facilitate cleaning.
Motors
If a motor is mounted internal to the ducting it must be a totally enclosed air over (TEAO) motor which will be cooled by the extracted air stream. If the motor is external or the fan is a bifurcated design then it must be a totally enclosed fan cooled (TEFC) motor. TEFC motors must not be specified for use in an environment with airborne grease. Drip proof or ODP motors are almost never suitable for kitchen extract systems.
Motors should be specified according to their load requirements. Over sized motors allow for flexibility should blade adjustment ever be required but higher ongoing running costs are incurred. The efficiency of AC induction motors decreases as they are run further away from their full load capability. This means that if the absorbed power of a fan blade set is 2 Kilowatts, it will consume more electricity if a 3 Kilowatt motor is used instead of a 2.2 Kilowatt motor to do the same work.
Motors other than the usual AC induction motors are beginning to appear in extraction systems;
Electronically commutated motors (ECM) are occasionally encountered. These motors are actually a DC motor which converts the AC supply voltage to DC internally. This type of motor requires complicated internal electronic controls to run but they do allow for easy speed control and have very high efficiency performance. As a newer technology, the price of these motors is still somewhat prohibitive and there is a limit to the maximum sixes available but with further development and higher sales figures this probably won’t be true for long.
External rotor motors are becoming common equipment on all genres of fans. This type of motor is often incorporated as an integral part of the blade set hub and, as which, cannot usually be repaired. This would mean that motor failure will require a complete fan replacement. They are almost always used in direct drive configuration and can also be found as a removable item in some fan units. Their main advantage is in their compact design allowing the overall dimensions of the fan unit to be reduced. They are also sometimes manufactured specifically to be exactly matched to the blade set they are supplied with to allow for greater efficiency which means they are made in uncommon Kilowatt sizes. This can only be done with centrifugal blades with non overloading characteristics.
Commercial extractor hood fan motors would usually have overload protection on their electrical supply. The overload protector will trip if the fan should ever become jammed or if one phase of the electrical supply ever fail and would usually be manually resettable once the fault has been remedied.
Modern fans and motors are usually manufactured with sealed and maintenance free bearings. These bearings require no cleaning or re greasing and are disposable should they ever become noisy, or suffer catastrophic failure.
Some larger fans utilize a pillow block bearing or plummer block bearings. These bearings require regular maintenance in the form of alignment checking and re greasing.
Common causes of failure of these bearings are;
Over greasing where the grease quantity in the bearing is too high and causes hydraulic locking inside the bearing under high acceleration conditions. This can cause irreparable damage to the bearing internal components or high running temperatures resulting in shortened lifespan. Bearings should only be 30 - 50% filled with grease depending on manufacturers specs.
Failure of the shaft seals allowing the grease to escape from the bearing and the ingress of dirt which acts as an abrasive compound when mixed with the bearing grease and causes friction damage and accelerated wear.
Over-tensioning of drive belts which increases the mechanical load on the bearing and the heat produced internally. This also causes premature wear and tear. This problem is common where contractors have increased belt tension to stop squealing on start-up.
Incorrect bearing lubricant generally shortens the lifespan of the bearings by either the lubricant itself breaking down or by the lubricant chemically attacking the rubber seals. The lubricant used must be matched to the type of bearing and the application it is used in.
Bearing rotor voltage discharge. This can occur with a motor supplied by a variable-frequency drive, the high rates of change of the motor supply voltage produced by the IGBT output with respect to time (i.e. high dv/dt rate) which, via capacitive coupling across the rotor/stator air gap, can induce voltages into the rotor. If the rotor is at a different potential to the motor chassis then this voltage will cause current flow via the route of least resistance to the chassis ground. The route of least resistance is usually the bearing. As the voltage discharges in pulses it leaves microscopic pits in the bearing race, this increases friction and leads to bearing failure. Rotor earthing kits are now commercially available to combat this problem.
Poor manufacture quality. Increasingly large numbers of cheap ‘no name’ bearings are available, even through some of the supposedly respectably distributors. Brand name piracy is also all too common where a low quality bearing is packaged as a high quality brand name.
There are 2 major applications of extractor hoods: ducted (or vented) application, and ductless (or recirculating) application. In a ducted application, the output collar of the extractor hood's blower motor is attached to a duct system, which terminates outside of the residence. In a ductless application, a filter containing activated charcoal is used to remove odor and smoke particles from the air, before releasing the cleaned air back into the kitchen environment.
A ducted application is generally preferable, since it allows for removal of all forms of airborne contamination, while ductless application recirculates heat and moisture into the kitchen environment. In addition, a ducted application eliminates the need for replacing the activated charcoal filters on a regular basis, and avoids the airflow restriction (and resultant loss of power) caused by activated charcoal filter placement. However, some kitchen environments do not allow ducted application, due to lack of space or ability to install a duct system, make-up air requirements, or the additional cost of heating/cooling the make-up air.
Some range hood designs allow for both types of applications, and are typically noted as such in the manufacturer's product literature.
Exhaust hoods almost always include built-in lighting (incandescent, fluorescent, or halogen) to illuminate the cooking surface. In addition, some manufacturers offer matching accessories, such as: backsplash panels, shelf units, dish racks, and other attachments, allowing a greater flexibility of design.
The invention of various forms of extractor hood in mid 20th century allowed for the reintroduction of the Farmhouse kitchen into popular architecture.
Commercial extractor hoods are generally hung high enough for people to walk underneath them without injury. They should be sized to overlap the footprint of the cooking equipment they cover by at least 200mm in every direction. This is to prevent smoke spillage from the hood during high kitchen output times.
Various methods are used by hood manufacturers to direct the polluted air plume efficiently into the hood. The shape and layout of the filter bank, the method and direction of make-up air supply and various skirts and baffles in the path of the airflow are three common techniques.
An important part of the extraction hood system is the separate make-up air system. If the correct amount of make-up air is supplied back into the kitchen it allows the extraction system to remove the polluted air plume with greater ease. Make-up air should replace around 85-90% of the volume of air being extracted, this is to keep the kitchen at a slightly negative air pressure compared to the surrounding areas. This negative pressure helps contain fires in the kitchen should they occur and prevents the restaurant decor being coated in a film of grease by air migrating from the kitchen into surrounding areas. The make-up air system should be run hand in hand with the extractor hood at all times. The make-up air should be supplied evenly around the outside of the area covered by the extractor hood. It should be introduced into the kitchen at a low velocity and with the minimum turbulence possible in order to prevent cross draughts under the extractor hood.
Recent developments in commercial kitchen extraction hoods include the use of ultra violet light as an alternative to activated carbon filters for the final filtration stage. Numerous low pressure quartz mercury vapour tubes are contained in the plenum box or upper area of the hood, in the path of the extracted air flow. These tubes produce high intensity UV light causing ozone to be produced in the immediate area. The UV light subjects the grease particles to photolysis, which alters them on a molecular level and ozonolysis which causes the particles to oxidize. The grease particles are converted to carbon in the form of a fine powder, CO2 and water vapour by this method. All these byproducts can be discharged safely and don't adhere to the internal surfaces of the ducting as the grease particles do. This reduces the fire hazard that is presented by kitchen extraction systems, especially when they are not subjected to regular degreasing and cleaning.
The UV system still requires efficient pre-filters in the canopy hood to remove grease particles 10 microns (micrometer) diameter and over. The UV light cannot penetrate these larger particles sufficiently to break them down. Without these filters the UV tubes become coated in grease residue making them rapidly ineffective and reducing their operating lifespan. Multiple safety devices should be installed on a UV-C system as human exposure to light in the UV-C range presents a serious safety hazard.
Canopy extraction hoods equipped with a UV system will have an associated electrical control panel. This panel will contain the switch gear required for the UV light tubes, the safety interlocking devices and indicator lamps to visually convey the condition of the system to the user.
A UV system can remove sufficient grease from the extracted plume to allow discharge of the air into a public open space. This can mean that locations previously considered unsuitable for a restaurant due to air pollution issues might be viable with this type of system.
The disadvantages of a UV system include the high cost and limited life (usually around 4000 hours depending on manufacturer) of the UV tubes as well as the UV system will require regular servicing by qualified personnel. The UV tubes often contain small amounts of mercury meaning specialist disposal or recycling may be necessary
The UV canopy hoods have been available for commercial restaurant, hospital and hotel installations for several years manufactured by companies such as Vent Master and Halton.
A commercial extractor hood will usually be ducted to the roof of the premises where it discharges. Discharge is usually vertical in an upward direction to allow any unfiltered smoke, water vapour and odors to become rapidly dispersed without unsociable effects to neighbors. The vertical discharge unit (VDU) is a device that is mounted on top of the ducting. It performs several functions such as increasing the discharge air velocity to encourage dispersing, providing a weather-proof cover to prevent rain, birds and debris entering the ducting and sound attenuation. VDU's are generally constructed from fiberglass, galvanized mild steel, stainless steel or a combination of the three.
Commercial extractor hood ducting should be constructed from thick gauge welded mild steel unlike HVAC ducting which is generally made from galvanized thin gauge sheet with folded joints. This is to provide greater fire resilience and to prevent grease that coats the inside leaking out through the joints. Access panels and frames are often fitted every few meters to facilitate periodic cleaning of the inside of the duct work.
The first extraction hood was produced by Faber in 1963.
Today's major manufacturers of extractor hoods include: Broan, Elica, Faber, Futuro Futuro, Gaggenau , Independent, and Vent-A-Hood. Each of those manufacturers offers a distinctive style, selection of materials, and price range. In addition, some of these manufacturers offer proprietary technological advances, such as:
Elica's "Elica Deep Space" noise reduction system
Futuro Futuro's "FaSteel" fingerprint-free stainless steel
Gaggenau's "Coanda Effect" airflow direction system
Vent-A-Hood's "Magic Lung" baffle filter/blower system
Extractor hoods may be made from a variety of materials, including: copper, steel, tempered glass, wood, aluminum, brass, heat-resistant plastics, and more.
Control systems for extractor hoods are typically electronic in nature. However, electromechanical controls (relatively rare on mid-market and high-end models) exist as well. Extractor hoods with electronic control systems may offer one or more of the following features: remote control, motorized height adjustment, thermal sensor, overheat protection, boost mode, delayed shut-off, filter cleaning reminder, active noise cancellation, temperature display, user presets (memory), or a combination of the above.
Prices for residential extractor hoods can range from US $100 to US $20,000 or more for custom-built models. The majority of products is located in the US $400 - US $2500 range (according to results from major online sources, including Google Base, Epinions.com, PriceGrabber.com, and other popular review sites.)